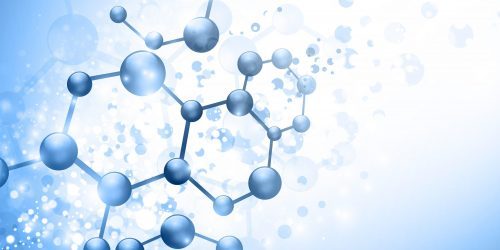
प्राकृतिक अभियन्त्रिक सामग्री तथा योगात्मक विनिर्माण
सीएसआईआर-एम्प्री एक दशक से पॉलिमर कंपोजिट के विकास पर सक्रिय रूप से काम कर रहा है| भोपाल के पास उद्योगों को समर्थन देने के लिए विभिन्न सामग्रियों और प्रक्रियाओं का उपयोग करके डिजाइन, सिमुलेशन और उत्पाद विकास पर अनुभव रखता है। 12वीं योजना परियोजना के दौरान, हमने सीएनटी प्रबलित शेप मेमोरी पॉलिमर कंपोजिट और इसके अनुप्रयोगों को विकसित करने में सक्रिय रूप से भाग लिया है। हमने उच्च शक्ति वाले इन्सुलेटिंग पॉलिमर कंपोजिट भी विकसित किए हैं। वर्ष 2015 में, हमने आरटीपी-सीवीडी के माध्यम से सिंगल लेयर ग्राफीन (हनीकॉम्ब लैटिस में व्यवस्थित कार्बन का 2डी एलोट्रोप) बनाने पर काम करना शुरू किया। नई उभरती विनिर्माण प्रौद्योगिकियों में एएमपीआरआई का नेतृत्व करने के लिए, हमने 3डी प्रिंटिंग प्रौद्योगिकियों के माध्यम से ग्राफीन आधारित मिश्रित सामग्री और घटकों को विकसित करने की हालिया पहल की है। दूसरी दिशा में हमारे वैज्ञानिक परमाणु आणविक गतिशीलता सिमुलेशन, परिमित तत्व सिमुलेशन और विफलता विश्लेषण पर भी काम कर रहे हैं। समूह में मजबूत वैज्ञानिक और तकनीकी कर्मचारी और इंजीनियरिंग और विज्ञान के बहु-विषयक पृष्ठभूमि के एसीएसआईआर छात्र शामिल हैं जो सामग्री विज्ञान और प्रक्रियाओं पर अत्याधुनिक शोध पर काम कर रहे हैं।
सीएनटी प्रबलित आकार मेमोरी पॉलिमर कंपोजिट
शेप मेमोरी मटेरियल स्मार्ट सामग्रियों का एक वर्ग है जो उपयुक्त उत्तेजना लागू होने तक अस्थायी आकार धारण करने में सक्षम होते हैं जिसके बाद वे अपने मूल स्थायी आकार को पुनः प्राप्त कर लेते हैं। 12वीं FYP के प्रोजेक्ट के तहत “इंजीनियरिंग अनुप्रयोगों के लिए थर्मो रिस्पॉन्सिव और मैग्नेटिक शेप मेमोरी सामग्री और उपकरणों के डिजाइन और विकास” पर शेप मेमोरी पॉलिमर कंपोजिट में सुधार की एक गतिविधि शुरू की गई थी। विभिन्न इंजीनियरिंग अनुप्रयोगों के लिए शेप मेमोरी पॉलिमर (एसएमपी) का बड़े पैमाने पर अध्ययन किया जा रहा है। एसएमपी के लिए उत्तेजनाओं में गर्मी, नमी, विलायक या पीएच मान में परिवर्तन, प्रकाश, तनाव आदि शामिल हैं। एसएमपी में असाधारण उच्च पुनर्प्राप्ति तनाव होता है लेकिन उनके कम पुनर्प्राप्ति-तनाव, थर्मल और विद्युत इन्सुलेशन के परिणामस्वरूप सीमित अनुप्रयोग होते हैं। क्रॉस-लिंकिंग घनत्व को बढ़ाने, पॉलिमर मैट्रिक्स में अकार्बनिक फिलर्स को जोड़ने, पॉलिमर रसायन विज्ञान को बदलने या विरूपण स्थितियों को बदलने आदि जैसे तरीकों को लोचदार मापांक को बढ़ाने और बदले में एसएमपी की वसूली तनाव को बढ़ाने के लिए अपनाया गया है। सीएसआईआर-एम्प्री में उनके यांत्रिक और विद्युत गुणों में सुधार के लिए सीएनटी के साथ एसएमपी के सुदृढीकरण की जांच की गई है।
नमूनों में आकार स्मृति प्रभाव पारंपरिक थर्मो मैकेनिकल चक्र, साथ ही पीएसआरएस (प्रोग्रेसिव स्ट्रेच-रिलैक्स-स्ट्रेच) चक्र के रूप में नामित एक संशोधित थर्मो मैकेनिकल चक्र का उपयोग करके देखा गया था। पारंपरिक एसएमसीपी में शामिल है; i) नमूने को TH तक गर्म करना जो कांच के संक्रमण तापमान, Tg से अधिक है, ii) एक निश्चित स्तर तक विकृत/खिंचाव, iii) विरूपण तनाव को कम किए बिना तापमान को Tg से नीचे लाना, iv) लगाए गए तनाव (क्लैंप इत्यादि) को हटाना और नमूने को आराम करने और एक निश्चित लंबाई, एलएफ, या एक अस्थायी आकार प्राप्त करने की अनुमति देना। नमूना अब आकृति स्मृति प्रभावों का मूल्यांकन करने के लिए तैयार है क्योंकि नमूने में आकृति स्मृति बनाई गई है। जैसा कि चरण (ii) में बताया गया है, पारंपरिक एसएमसीपी में नमूने को तापमान TH पर एक निश्चित लंबाई ls तक लगातार बढ़ाया गया था, जबकि संशोधित SMCP के तहत विरूपण चरण (ii) को विरूपण की PSRS योजना के साथ बदल दिया गया था। तदनुसार, चरण (ii) में अधिकतम तनाव रुक-रुक कर छूट के साथ कई चरणों में प्राप्त किया गया था। दूसरे शब्दों में, छोटे तनाव के बाद विश्राम और खिंचाव होता है, और उसके बाद दूसरा विश्राम और खिंचाव होता है। यह प्रक्रिया तब तक जारी रहती है जब तक अधिकतम डिज़ाइन किया गया तनाव प्राप्त नहीं हो जाता। चरण (iii) और (iv) पॉलिमरिक सामग्रियों में आकार स्मृति बनाने की पारंपरिक विधि के समान ही रहे।
अलग-अलग परीक्षण नमूने तैयार किए गए और उन्हें एसएमपीयू, पीयूसीएनटी1, पीयूसीएनटी2, पीयूसीएनटी3 और पीयूसीएनटी4 के रूप में नामित किया गया, जिसमें एसएमपीयू में क्रमशः 0, 0.063, 0.125, 0.188 और 0.250 पीएचआर एमडब्ल्यूसीएनटी थे। चित्र-1 आकार मेमोरी पॉलिमर के विकास और लक्षण वर्णन की पीएसआरएस योजना के अनुरूप पॉलीयुरेथेन (एसएमपीयू) नमूनों के तीन तनाव तनाव वक्र और तीन पुनर्प्राप्ति तनाव तनाव वक्र दिखाता है। अधिकतम तनाव तीन चरणों में प्राप्त किया गया; पहले नमूने को 17% तक बढ़ाया गया और शिथिल किया गया, फिर 34% तक बढ़ाया गया और शिथिल किया गया, अंत में तीसरे चरण में नमूने को 51% तक बढ़ाया गया। उन्हें एक अस्थायी आकार तय करने की अनुमति देने के बाद, मानक प्रक्रिया के अनुसार पुनर्प्राप्ति तनाव निर्धारित किया गया था। 70oC पर SMPU का पुनर्प्राप्ति तनाव 1.09 MPa देखा गया। इस मामले में स्ट्रेन रिकवरी 77.75% थी। इसी प्रकार चित्र 2 आकार मेमोरी पॉलिमर के विकास और लक्षण वर्णन की पीएसआरएस योजना के अनुरूप सीएनटी प्रबलित पॉलीयूरेथेन (पीयूसीएनटी1) नमूनों के तीन तनाव तनाव वक्र और तीन पुनर्प्राप्ति तनाव तनाव वक्र दिखाता है।
चित्र 1) पारंपरिक विधि और 2) पीएसआरएस विधि द्वारा विभिन्न तनावों पर विकृत नमूनों की पुनर्प्राप्ति तनाव को दर्शाता है। नमूनों को पारंपरिक और पीएसआरएस विधि द्वारा 70oC पर अधिकतम (51%) तनाव तक बढ़ाया गया था। फैलाए गए नमूनों को परिवेश के तापमान पर लाया गया, और आराम दिया गया। एक बार जब नमूनों को 70oC पर लाया गया तो पुनर्प्राप्ति तनाव को विकृत तनाव के अनुरूप मापा गया और निरंतर तनाव दर के साथ तनाव को धीरे-धीरे कम किया गया। एसएमपीयू, पीयूसीएनटी1, पीयूसीएनटी2 और पीयूसीएनटी3 का पुनर्प्राप्ति तनाव पीएसआरएस के लिए क्रमशः 1.04, 1.14, 1.58 और 2.11 एमपीए और पारंपरिक विरूपण के लिए क्रमशः 0.88, 1.06, 1.55 और 1.97 एमपीए पाया गया। पारंपरिक स्कीम की तुलना में पीएसआरएस स्कीम में पुनर्प्राप्ति तनाव में उच्च मूल्य देखे गए।
एक उच्च यांत्रिक शक्ति पर्यावरण अनुकूल विद्युत इन्सुलेशन
प्राकृतिक फाइबर आधारित विद्युत इन्सुलेशन सामग्री अपनी पर्यावरण-मित्रता और बायोडिग्रेडेबिलिटी के कारण पारंपरिक विद्युत इन्सुलेशन का विकल्प प्रदान करती है। जहां विद्युत और यांत्रिक गुणों के संयोजन की आवश्यकता होती है, वहां आवेदन के लिए सिसल फाइबर सबसे आशाजनक प्राकृतिक फाइबर में से एक है। विभिन्न फाइब्रिल लोडिंग कंपोजिट के साथ सिसल फाइब्रिल आधारित एपॉक्सी कंपोजिट का उपयोग किया जा सकता है जहां अधिकतम यांत्रिक शक्ति और अच्छे विद्युत इन्सुलेशन की आवश्यकता होती है जैसे ट्रांसफार्मर में प्रेस बोर्ड और ट्रांसफार्मर निर्माण में उपयोग की जाने वाली इसकी असेंबली।
वांछित परिणाम प्राप्त करने के लिए सिसल फाइब्रिल्स को 5% NaOH विलयन द्वारा उपचारित किया गया। अनुपचारित सिसल फाइब्रिल प्रबलित एपॉक्सी (यूएसएफई) और उपचारित सिसल फाइब्रिल प्रबलित एपॉक्सी (टीएसएफई) कंपोजिट के यांत्रिक और विद्युत गुणों का मूल्यांकन किया गया। टीएसएफई कंपोजिट के अचालक स्थिरांक ɛ’ और अपव्यय कारक tanδ पर आवृत्ति भिन्नता का प्रभाव भी विभिन्न फाइब्रिल लोडिंग के लिए दिखाया गया है; 10, 20, 30 और 35 wt. %. परीक्षण कमरे के तापमान पर 1-10 किलोहर्ट्ज़ की आवृत्ति रेंज में किए गए। यह देखा गया कि टीएसएफई का अचालक स्थिरांक ɛ’ और अपव्यय कारक टैन क्रमशः बढ़ी हुई आवृत्ति चित्र 2 और चित्र 3 के साथ कम हो गया था।
आरटीपी-सीवीडी के माध्यम से सीयू फ़ॉइल पर उच्च गुणवत्ता वाली एकल परत ग्राफीन
पिछले वषों में हमने Cu फ़ॉइल पर उच्च गुणवत्ता वाली एकल परत ग्राफीन का सफलतापूर्वक प्रदर्शन किया है। विकसित प्रक्रिया अद्वितीय है और हमें सस्ती तकनीक के माध्यम से ग्राफीन बनाने में सक्षम बनाती है। भविष्य में ऐसी कम लागत वाली तकनीक विकसित करके ही हम अपनी कम लागत वाली रैपिड थर्मल प्रोसेसिंग – रासायनिक वाष्प जमाव (आरटीपी-सीवीडी) का विस्तार करके ग्राफीन फाइबर प्राप्त कर सकते हैं। इस वर्ष हमने कई प्रयोग किए हैं और एक इंच क्यू फ़ॉइल पर 90% से अधिक एकल परत ग्राफीन की वृद्धि के लिए परिणामों को अनुकूलित किया है। इसलिए हमने सिंगल लेयर ग्राफीन के विकास का प्रदर्शन किया है, अगला कदम बड़े क्षेत्र को Cu फ़ॉइल पर एक समान सिंगल लेयर ग्राफीन बनाना होगा। उगाए गए ग्राफीन बहुत उच्च गुणवत्ता वाले हैं और 2डी पीक और जी पीक की तीव्रता का अनुपात 4.0 के करीब है। जो Cu फ़ॉइल पर डिवाइस की गुणवत्ता वाले ग्राफीन को दर्शाता है। हमने ग्राफीन की गुणवत्ता की पुष्टि के लिए रमन मैपिंग के लिए आईआईएसईआर, भोपाल के साथ सहयोगात्मक शोध किया है। भविष्य में इसके अलावा उपकरण बनाने की आगे की प्रक्रिया और विभिन्न उपकरण बनाने के लिए ग्राफीन का उपयोग करना प्रस्तावित है।
ग्राफीन मिश्रित सामग्री से बनी उन्नत सूक्ष्म जाली संरचनाएँ (माइक्रो लेटिस स्ट्रक्चर)
हमने आरआरसीएटी, इंदौर के सहयोग से मेटल 3डी प्रिंटिंग का उपयोग किया है और ए एल /ग्राफीन कंपोजिट के लेजर मापदंडों को अनुकूलित करने पर काम किया है। लेजर एडिटिव मैन्युफैक्चरिंग (एलएएम) उन्नत विनिर्माण प्रौद्योगिकियों में से एक है जो सीएडी मॉडल से सीधे सामग्री की परत दर परत जमाव द्वारा बेहतर सामग्री गुणों के साथ जटिल इंजीनियरिंग घटकों का निर्माण करने में सक्षम है। सामग्री का परत-दर-परत जोड़ एलएएम को इंजीनियरिंग घटकों को आकार देने वाली सामग्री की पूर्व-परिभाषित संरचना के चयनात्मक जमाव में सशक्त बनाता है, जिससे यह एक सुविधा आधारित डिजाइन और विनिर्माण प्रौद्योगिकी बन जाती है। एलएएम निर्मित घटक काफी हद तक एलएएम प्रसंस्करण मापदंडों और एकल जमा परत की गुणवत्ता पर निर्भर करते हैं। इसलिए एलएएम निर्मित घटकों के बेहतर यांत्रिक गुणों को प्राप्त करने के लिए उपयुक्त प्रसंस्करण मापदंडों का चयन अनिवार्य आवश्यकताओं में से एक है। यह पेपर अल और एसएस सब्सट्रेट पर एल्यूमीनियम/ग्रैफेम (अल-जी) मिश्रित के एलएएम की रिपोर्ट करता है। सब्सट्रेट पर 2 मिमी लेजर बीम व्यास के साथ 2 किलोवाट फाइबर लेजर आधारित एडिटिव विनिर्माण का उपयोग लेजर स्कैनिंग गति और लेजर पावर के विभिन्न संयोजनों पर एएलजी परतों (एएल + 1% डब्ल्यूटी जी) को जमा करने के लिए किया गया था। जमा परतों की गुणवत्ता पर लेजर शक्ति और स्कैनिंग गति के प्रभाव की जांच की गई और इष्टतम पैरामीट्रिक विंडो की पहचान की गई। ऊर्जा तीव्रता की इष्टतम सीमा 50 से 400 जे/मिमी है जो सामग्री जमाव (<50पी/वी – <400 जे/मिमी) के लिए अनुकूल है। इस प्रकार तैयार नमूनों को ऑप्टिकल माइक्रोस्कोपी, स्कैनिंग इलेक्ट्रॉन माइक्रोस्कोपी और सूक्ष्म कठोरता माप के अधीन किया गया। एक अच्छी गुणवत्ता वाला निरंतर ट्रैक 108 जे/मिमी ऊर्जा तीव्रता पर देखा जाता है और एएल सब्सट्रेट पर कठोरता में बहुत मामूली बदलाव देखा जाता है)। एसएस सब्सट्रेट पर सूक्ष्म कठोरता में उल्लेखनीय वृद्धि देखी गई है। एचवी का अधिकतम मान 0.6 मीटर/मिनट पर 463.6 है। लेजर स्कैनिंग गति और 1.2 किलोवाट लेजर शक्ति। इन एलएएम निर्मित एल्यूमिनियम ग्रैफेम कंपोजिट में जटिल आकार और सेलुलर संरचना के निर्माण के लिए हल्के वजन और उच्च शक्ति सामग्री के क्षेत्र में संभावित अनुप्रयोग हैं।
एक धात्विक माइक्रोलैटिस आपस में जुड़े हुए खोखले स्ट्रट्स के एक नेटवर्क से बना होता है। धात्विक माइक्रोलैटिस की विशेषता बहुत कम घनत्व है। यांत्रिक रूप से, ये माइक्रोलैटिस व्यवहारिक रूप से इलास्टोमर्स के समान होते हैं और महत्वपूर्ण संपीड़न के बाद लगभग पूरी तरह से अपने आकार को पुनः प्राप्त कर लेते हैं। इससे उन्हें पहले के एरोजेल, जो भंगुर, कांच जैसे पदार्थ होते हैं, की तुलना में महत्वपूर्ण लाभ मिलता है। धात्विक सूक्ष्म जाली में यह इलास्टोमेरिक गुण इसके अलावा कुशल शॉक अवशोषण में परिणाम देता है। धात्विक माइक्रोलैटिस को थर्मल और कंपन इंसुलेटर जैसे शॉक अवशोषक के रूप में संभावित अनुप्रयोग मिल सकते हैं, और बैटरी इलेक्ट्रोड और उत्प्रेरक समर्थन के रूप में भी उपयोगी साबित हो सकते हैं। ऑटोमोटिव और वैमानिकी निर्माता बेहद हल्के और कुशल ढांचे विकसित करने के लिए माइक्रोलैटिस तकनीक का उपयोग कर रहे हैं जो उच्च प्रदर्शन वाले वाहनों के लिए संरचनात्मक सुदृढीकरण और गर्मी हस्तांतरण जैसे कई कार्यों को एकल घटकों में जोड़ते हैं। सीएसआईआर-एम्प्री में हमने विभिन्न सूक्ष्म जाली संरचनाओं को विकसित और 3डी प्रिंट किया है और इसके यांत्रिक गुणों का अध्ययन किया है।
हल्के वजन के अनुप्रयोगों के लिए नेवेल कैलाबी-यॉ आधारित सूक्ष्म जाली संरचनाएं विकसित की गई हैं। कैलाबी-यॉ मैनिफोल्ड एक अनूठी संरचना है जो विशेष रूप से बीजगणितीय ज्यामिति द्वारा बनाई गई है। इस विविधता की असाधारण सूक्ष्म वास्तुकला शोधकर्ता को संरचना के यांत्रिक गुणों की परिकल्पना करने के लिए उत्साहित करती है। संरचना के यांत्रिक गुणों की पहचान करने के लिए यह अध्ययन किया गया है। संरचना को गैंडा-ग्रासहॉपर पर कुछ ज्यामितीय मापदंडों जैसे आयाम (6डी, 7डी, 8डी, 9डी, 10डी) के साथ डिजाइन किया गया है और पीएलए सामग्री के साथ एफडीएम प्रिंटर द्वारा 3डी मुद्रित किया गया है। वज़न अनुपात की ताकत को कम करने के लिए जटिल ज्यामितीय संरचनाओं की सेलुलर सामग्री बनाना एडिटिव मैन्युफैक्चरिंग के लिए प्रमुख अनुप्रयोग हिस्सा है। इसके अलावा 3डी प्रिंटर का उपयोग समान सेलुलर ठोस पदार्थों के निर्माण के लिए किया जाता है, जिसमें अपेक्षाकृत कम द्रव्यमान, बेहतर ऊर्जा अवशोषण विशेषताओं के साथ उच्च शक्ति होती है, जो उन्हें उच्च मूल्य वाले एयरोस्पेस, चिकित्सा और इंजीनियरिंग अनुप्रयोगों के लिए उपयुक्त बनाती है।
तीव्र तापीय प्रसंस्करण – उच्च गुणवत्ता वाले बड़े क्षेत्र ग्राफीन का रासायनिक वाष्प जमाव (आरटीपी-सीवीडी) विकास
ग्राफीन ने अपनी अनूठी बैंड संरचना और इलेक्ट्रॉनिक गुणों के कारण काफी रुचि आकर्षित की है, जो इसे अगली पीढ़ी के इलेक्ट्रॉनिक उपकरणों, पारदर्शी, लचीले इलेक्ट्रोड, सेंसर और बहु-कार्यात्मक कंपोजिट के लिए आशाजनक उम्मीदवार बनाती है। इस विषय में, हम विभिन्न वाणिज्यिक स्रोतों और घरेलू ग्राफीन नमूनों से ग्राफीन के रमन लक्षण वर्णन के सामान्य विवरण पर चर्चा करते हैं। हम ग्राफीन लक्षण वर्णन के लिए मानकीकरण प्रक्रिया की आवश्यकता पर भी जोर देते हैं। एक अन्य चुनौतीपूर्ण क्षेत्र मिश्रित सामग्रियों में ग्राफीन का लक्षण वर्णन है, रमन ग्राफीन प्रबलित मिश्रित सामग्रियों के लक्षण वर्णन में महत्वपूर्ण भूमिका निभाता है। हम कंपोजिट बनाने से पहले ग्राफीन के लक्षण वर्णन के लिए महत्वपूर्ण उपकरण के रूप में मैपिंग के साथ रमन स्पेक्ट्रोस्कोपी का उपयोग करने और ग्राफीन की स्थिति और मैट्रिक्स के साथ इसके इंटरफ़ेस इंटरैक्शन पर विस्तार से चर्चा करते हैं। रैपिड थर्मल प्रोसेसिंग-केमिकल वेपर डिपोजिशन (आरटीपी-सीवीडी) प्रणाली द्वारा उगाए गए सिंगल लेयर ग्राफीन के एक रमन स्पेक्ट्रा ने 3.83 का I2D/IG अनुपात दिखाया है, जो बहुत उच्च गुणवत्ता वाले सिंगल लेयर ग्राफीन का संकेत देता है। ग्राफीन की आकृति विज्ञान की जांच के लिए मैपिंग के साथ विकसित फिल्मों को रमन स्पेक्ट्रोस्कोपी द्वारा चित्रित किया गया था। सतत तरंगिका परिवर्तन (सीडब्ल्यूटी) का उपयोग करके पृष्ठभूमि हटाने और रमन मैपिंग डेटा की गैर-रेखीय न्यूनतम वर्ग फिटिंग करने के लिए एक स्वचालित कार्यक्रम विकसित किया गया है।
An automated program has been developed to carry out background removal using Continuous Wavelet Transformation (CWT) and carry out non linear least square fitting of Raman mapping data.
एडिटिव मैन्युफैक्चरिंग द्वारा ग्राफीन प्रबलित एसएस + ग्राफीन कंपोजिट
इस कार्य में, हमने एक स्टील ग्राफीन कंपोजिट विकसित किया है जिसमें एक द्वि-आयामी ग्राफीन का उपयोग 3-आयामी सामग्रियों के लिए मजबूत एजेंट के रूप में किया जाता है, जो लगभग सभी प्रकार के मजबूत करने वाले एजेंट के लिए अच्छा विकल्प है। एकत्रीकरण की अत्यधिक प्रवृत्ति और घनत्व में बड़े अंतर के कारण ग्रेफीन को तरल पिघल में फैलाना बहुत मुश्किल है। इस कार्य में, हम जीएमएमसी बनाने के लिए वैकल्पिक प्रसंस्करण विधियों और प्रक्रिया अनुकूलन का उपयोग करते हैं। ग्राफीन में धातु सामग्री के साथ गीली होने की क्षमता बहुत कम होती है। धातु मैट्रिक्स के साथ एक अच्छा इंटरफेशियल बॉन्डिंग उच्च शक्ति वाले कंपोजिट बनाने की कुंजी है। मेटल मैट्रिक्स के साथ ग्राफीन के गीले व्यवहार को समझने के लिए एक विस्तृत अध्ययन की आवश्यकता है। इसके अलावा धातु और मिश्र धातुओं में ग्राफीन को सफलतापूर्वक शामिल करने के लिए सामग्रियों के सतही संशोधनों और प्रक्रिया संशोधनों का विस्तार से अध्ययन करने की आवश्यकता है। ग्राफीन मधुकोश जाली में व्यवस्थित कार्बन की एक एकल परमाणु परत है जो 2डी सामग्री है। ग्राफीन के गुणों का उपयोग करने के लिए, हमें जीएमएमसी को सफलतापूर्वक संश्लेषित करने के लिए आउटबॉक्स प्रसंस्करण विधियों को विकसित करने की आवश्यकता है। और यही इस कार्य का उद्देश्य है I एसपी बढ़ाने के लिए. स्टील/ग्राफीन मिश्रित बनाकर इसकी संक्षारण प्रतिरोध संपत्ति को प्रभावित किए बिना स्टील की ताकत। संक्षारण, यांत्रिक, थर्मल और विद्युत गुणों पर ग्राफीन संरचना के प्रभावों का अध्ययन करें। उच्च शक्ति ग्राफीन + स्टील कंपोजिट बनाने के लिए लेजर आधारित मेटल एडिटिव मैन्युफैक्चरिंग सिस्टम के मापदंडों को अनुकूलित करें।