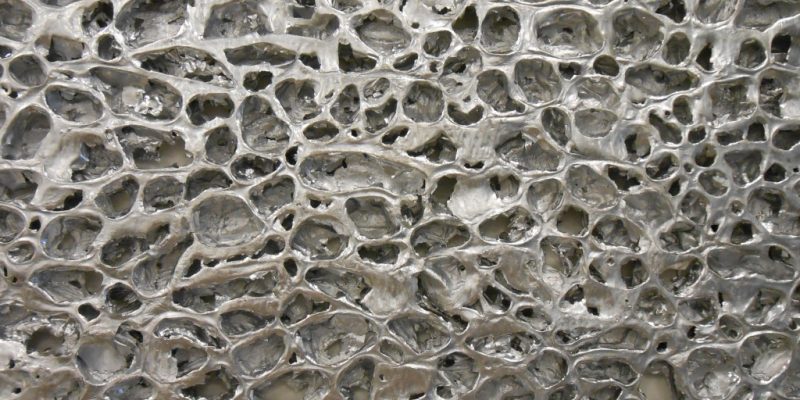
हल्के वजन वाले उच्च प्रदर्शन धातु सामग्री के विकास में एम्प्री की गतिविधियों में एल्यूमीनियम मेटल मैट्रिक्स कंपोजिट (एएल एमएमसी), समान सेल आकार और वितरण के साथ एल्यूमीनियम फोम, घटकों का विकास, जैसे कि एएल एमएमसी ब्रेक ड्रम, एएल फोम भरे क्रैश बॉक्स, एएल भरे सैंडविच पैनल, एमजी मिश्र धातु केसिंग आदि शामिल हैं। अल्ट्रासोनिक कंपन के बाद विद्युत चुम्बकीय स्ट्रिंग के माध्यम से अल्ट्राफाइन कण प्रबलित एएल एमएमसी विकसित करने की सुविधाएं स्थापित की जा रही हैं। ऑटोमोबाइल क्षेत्र के लिए हल्के वजन वाले धातु घटकों को विकसित करने के लिए उपयोग की जाने वाली प्रेशर डाई-कास्टिंग, अर्ध ठोस प्रसंस्करण आदि की सुविधाएं भी जोड़ी जा रही हैं। ए एल और एमजी मिश्र धातुओं और उनके मिश्रण के प्रसंस्करण के लिए माध्यमिक प्रसंस्करण, जैसे गर्म और ठंडा रोलिंग, एक्सट्रूज़न सुविधाएं स्थापित की गई हैं। कुछ नवीनतम कार्य हैं।
उच्च दबाव डाई कास्टिंग के माध्यम से अल-सीआईसी मिश्रित ब्रेक ड्रम:
एल्यूमीनियम मिश्र धातु, मेटल मैट्रिक्स कंपोजिट (एएल एमएमसी) आजकल काफी औद्योगिकियों और वैज्ञानिकों का ध्यान आकर्षित कर रहे हैं। एएलएमएमसी में प्रमुख सीमाएं गुरुत्वाकर्षण मार्ग द्वारा कास्टिंग है, जो उनके इंजीनियरिंग अनुप्रयोग को सीमित करती है और मोल्ड में पिघल को तेजी से डालने और जमने की उच्च दर के माध्यम से उनकी विशेषताओं/प्रदर्शन में सुधार किया जा सकता है। इस प्रकार प्रेशर डाई कास्टिंग द्वारा दबावयुक्त ठोसीकरण एक बहुत ही संभावित तकनीक हो सकती है। एएल एमएमसी के दबाव डाई कास्टिंग का अतीत में बहुत सीमित सीमा तक पता लगाया गया है और इसलिए सामग्री प्रणाली के साथ-साथ व्यवहार में प्रसंस्करण तकनीक के लाभों को प्राप्त करने के लिए इंजेक्शन दबाव, तापमान और समय इत्यादि जैसे विभिन्न प्रसंस्करण मापदंडों को अलग-अलग करके व्यवस्थित रूप से अध्ययन करने की आवश्यकता है। इसलिए किए गए वर्तमान कार्य में प्रेशर डाई कास्टिंग तकनीक का उपयोग करके एएल एमएमसी ब्रेक ड्रम का विकास शामिल है जो अंततः अच्छी गुणवत्ता वाले कास्टिंग/घटक प्राप्त करने में सक्षम हो सकता है।
वर्तमान कार्य में SiC कणों के इष्टतम प्रतिशत के साथ दो मिश्रधातुओं की संरचना का प्रयास किया गया है। विभिन्न भौतिक, यांत्रिक, थर्मल और पहनने के गुणों के लिए इन सामग्रियों का लक्षण वर्णन किया गया है। ब्रेक ड्रम की कास्टिंग का अनुकरण भी किया गया है। सबसे पहले मौजूदा डाई कास्ट ब्रेक ड्रम का ठोस मॉडलिंग ABAQUS, सॉफ्टवेयर का उपयोग करके तैयार किया गया है। फिर इसे प्रेशर डाई कास्टिंग सिमुलेशन करने के लिए कास्टिंग सॉफ्टवेयर में लिया जाता है। चूंकि ब्रेक ड्रम बाजार में उपलब्ध कच्चे लोहे का होता है, जिसे एएलएमएमसी ब्रेक ड्रम से बदला जाना है, इन दोनों सामग्रियों को वर्तमान कास्टिंग सिमुलेशन में माना जाता है। इसलिए इन सामग्रियों का उपयोग करके दो अलग-अलग कास्टिंग सिमुलेशन किए गए हैं। विभिन्न चरणों में ब्रेक ड्रम के जमने के क्षेत्र भी देखे गए। अंतिम ठोसकरण क्षेत्र की तुलना सिमुलेशन परिणामों में पाए गए ब्रेक ड्रम के अधिकतम तनाव क्षेत्र से की जाती है।
कच्चा लोहा और एल्यूमीनियम धातु मैट्रिक्स मिश्रित प्लेटों का घिसाव परीक्षण 5 मिनट, 10 मिनट, 15 मिनट और 20 मिनट के अलग-अलग समय के लिए किया गया। तापमान में वृद्धि और शीतलन परिणामों की दर का भी अध्ययन किया गया। मौजूदा कच्चा लोहा सामग्री के घिसाव गुण परिणाम की तुलना विकसित एएलएमएमसी सामग्रियों से की जाती है। ये घिसाव परीक्षण ब्रेकिंग सामग्री के विरुद्ध किए गए थे। घिसाव के गुणों के परीक्षणों की अंडरस्टेंडिंग से ब्रेक ड्रम में विकसित एएलएमएमसी सामग्री के उपयोग में मदद मिलेगी।
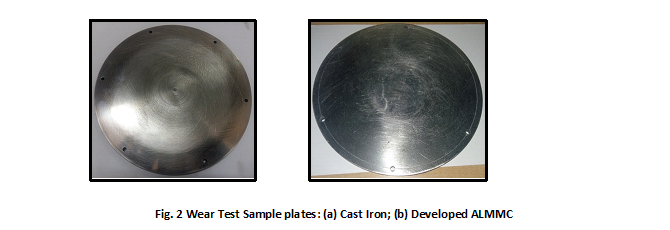
एनएसटीएल, विशाखट्टनम द्वारा निर्दिष्ट टॉरपीडो के लिए अल-सीआईसी नोज कोन:
नोज कोन के लिए आयाम और गुणों की व्यवस्था एनएसटीएल द्वारा दी गई है। मिश्रित सामग्री (LM13-10% SiC कण) को स्टिर कास्टिंग तकनीक का उपयोग करके डिजाइन और संश्लेषित किया गया है। कंपोजिट ने 140 एमपीए की फल क्षमता (यील्ड) प्रदर्शित की है । कंपोजिट की अवमंदन (डेम्पिंग) क्षमता की जांच की गई| सामग्री के लक्षण वर्णन और एनएसटीएल की आवश्यकता को पूरा करने के बाद, घटक बनाया गया है। अंततः एनएसटीएल द्वारा घटक का लीक प्रूफ़ के लिए परीक्षण किया गया है। प्रदर्शन मूल्यांकन के लिए एनएसटीएल को प्रोटोटाइप की आपूर्ति की गई ।
जैव-प्रत्यारोपण अनुप्रयोगों के लिए जैव सक्रिय टीआई-आधारित पोरस कंपोजिट:
पाउडर धातुकर्म तकनीक का उपयोग करके अलग-अलग आकार और आयतन अंशों के सेनोस्फीयर का उपयोग करके आई-सेनोस्फीयर सिंटैक्टिक फोम बनाए गए थे। फोम को यांत्रिक गुणों और सूक्ष्म संरचनाओं के संदर्भ में चित्रित किया गया था। 50% सेनोस्फेयर वाले फोम ने 250-300 एमपीए की ताकत प्रदर्शित की। इसका मापांक 15 से 30 GPa की सीमा में भिन्न होता है। संक्षारण व्यवहार को समझने के लिए समान फोम की विशेषता बताई गई है। इन फोम ने हैंक के घोल में उत्कृष्ट संक्षारण प्रतिरोध प्रदर्शित किया। एचएपी कोटिंग के साथ और बिना टी-सेनोस्फीयर फोम का उपयोग इनविट्रो परीक्षणों (सेल व्यवहार्यता) के लिए किया गया था। इसके अलावा, इन फोम की कोशिका या ऊतक के आसंजन के लिए जांच की गई। यह देखा गया है कि 50% सेनोस्फीयर और 250 माइक्रोन के सेल आकार वाले टीआई-फोम ने बेहतर सेल व्यवहार्यता और सेल पालन प्रदर्शित किया है। एचएपी कोटिंग ने बेहतर सेल व्यवहार्यता प्रदर्शित की।
अल-सेनोस्फीयर सिंटैक्टिक फोम बनाने के लिए सेनोस्फेयर का उपयोग:
थर्मल पावर प्लांट के अपशिष्ट फ्लाई ऐश से विभिन्न आकार श्रेणियों के सेनोस्फेयर निकाले गए। ये सेनोस्फेयर खोखले गोले हैं जिनमें मुख्य रूप से एल्युमिनो-सिलिकेट चरण होते हैं। ये 1000oC तक स्थिर होते हैं और गोले मजबूत होते हैं। इन्हें देखते हुए थर्मल पावर प्लांट के कम लागत वाले उप-उत्पाद का उपयोग एल्युमीनियम मिश्रधातुओं में सूक्ष्म-छिद्र निर्माण के रूप में एल्युमीनियम सेनोस्फीयर सिंटैक्टिक फोम बनाने के लिए किया गया था। एल्यूमीनियम सेनोस्फीयर सिंटैक्टिक फोम का घनत्व लगभग 1.9 ग्राम/सीसी तक कम होता है। एल्युमीनियम सेनोस्फीयर सिंटैक्टिक फोम के पिघलने के बाद जमने से कार्यात्मक रूप से वर्गीकृत वाक्यात्मक फोम उत्पत्ति होती है। इन फोमों का विद्युतचुंबकीय परिरक्षण के लिए आगे परीक्षण किया गया और पाया गया कि एल्यूमीनियम मिश्र धातु की तुलना में इनमें ईएमआई परिरक्षण में सुधार हुआ है। अवशोषण गुणांक भी मिश्र धातु की तुलना में बहुत अधिक है। अल-सेनोस्फीयर सिंटैक्टिक फोम की सूक्ष्म संरचना कार्यात्मक रूप से वर्गीकृत अल-सेनोस्फीयर फोम बिलेट।
अल-सेनोस्फीयर सिंटैक्टिक फोम की सूक्ष्म संरचना, कार्यात्मक रूप से वर्गीकृत अल-सेनोस्फीयर फोम बिलेट
हड्डी-मचान और निस्पंदन के लिए टीआई-फोम अनुप्रयोग:
40 से 80% छिद्र और 50 से 250 माइक्रोन सेल आकार वाले ओपन सेल टीआई-फोम पाउडर धातुकर्म तकनीक के माध्यम से बनाए गए थे। छिद्र समान रूप से वितरित होते हैं और सटीक रूप से नियंत्रित होते हैं। इन फोम की संपीड़न उपज शक्ति और मापांक छिद्र आकार और सरंध्रता की सीमा के आधार पर क्रमशः 20 से 350 एमपीए और 12 से 40 जीपीए की सीमा में पाए गए। इन फोम के इनविट्रो परीक्षण विभिन्न सेल लाइनर्स का उपयोग करके किए गए थे। यह ध्यान दिया गया है कि 250 माइक्रोन सेल आकार और 50 से 60% सरंध्रता वाले फोम ने उत्कृष्ट सेल व्यवहार्यता और सेल प्रसार का प्रदर्शन किया। संक्षारण परीक्षण दर्शाता है कि ये फोम हमारे बायोफ्लुइड के खिलाफ अत्यधिक संक्षारण प्रतिरोधी हैं। ऐसे सभी लक्षण वर्णन के बाद, इन फोम को एच ए पी के साथ लेपित किया गया और समान परीक्षण किए गए। जिसमें इनका बेहतर प्रदर्शन देखा गया| अंततः इन फोमों का निस्पंदन हेतु परीक्षण भी किया गया। इन Ti- या SS फोम ने अच्छी निस्पंदन क्षमता प्रदर्शित की। प्रोटोटाइप फ़िल्टर और संभावित जैव-प्रत्यारोपण प्रयोगशाला में अनुकूलित प्रक्रिया मापदंडों का उपयोग करके बनाए जाते हैं।
क्रैश योग्यता (पात्रता) अनुप्रयोगों के लिए एल्यूमिनियम फोम:
सीएसआईआर-एम्प्री ने दुर्घटना-योग्य अनुप्रयोगों के लिए लागत प्रभावी उच्च शक्ति और ऊर्जा अवशोषित एल्यूमीनियम फोम बनाने के लिए गतिविधि शुरू की है। एल्यूमीनियम फोम का उच्च तनाव दर परीक्षण 0.7 ग्राम/सीसी (छवि) के घनत्व के लिए 1500 एस-1 की तनाव दर पर 45 एमपीए का पठारी तनाव प्रदर्शित करता है। एल्यूमीनियम फोम से भरे क्रैश बॉक्स ने ऊर्जा अवशोषण में 100% सुधार प्रदर्शित किया। एआरएआई, पुणे में परीक्षण में कहा गया है कि 1000 ग्राम के क्रैश बॉक्स में 400 ग्राम एल्यूमीनियम फोम भरने से 54 किमी/घंटा की गति पर ऊर्जा अवशोषण 9.9 केजे से 19.9 केजे तक बढ़ गया (चित्र)। यह 750 किलोग्राम वजन वाली कार की प्रभाव ऊर्जा को कम करने के लिए पर्याप्त है। इस प्रकार ट्रेन दुर्घटनाओं के कारण होने वाले नुकसान से बचने के लिए इन फोम का उपयोग रेल जैसे अन्य परिवहन क्षेत्रों में भी उत्कृष्ट रूप से किया जा सकता है। विस्फोट प्रतिरोध अनुप्रयोगों के लिए ये उत्कृष्ट सामग्री हो सकती हैं। एम्प्री, भोपाल ने बड़े पैमाने पर विभिन्न घनत्व वाले फोम बनाने की क्षमता विकसित की है।